CIWH can be suppressed by adding a small amount of non-condensible gas.
Introduction
Condensate Induced Waterhammer (CIWH) is a potentially damaging phenomna where steam is mixed with cold water in piping (Grifitth, 1997). Of the five different types of CIWH (Izenson, 1988), the introduction of steam to a long run of horizontal piping that is full of cold water is the most damaging. At atmospheric steam pressure (such as the startup of a steam line) the phenomena is alarming but not usually dangerous. I have witnessed CIWH in an Ethylene Plant where steam from flashed condensate was mixed with subcooled condensate (40 C and 10 kPag). The the consequence was a loud BANG, akin to a 12 gauge shotgun blast every 10 seconds, and the 8 inch condensate line bounced slightly off the pipe supports. At high pressures, however, the consequences can be devestating. The 2007 steam pipeline accident at the MEG Energy SAGD facility (ERCB Report, 2008) occurred where high-pressure steam was introduced to the pipeline which contained water at nominally 100 C. The incident destroyed several hundred meters of steam pipeline. There were no injuries.
The standard method to avoid CIWH is to ensure that water is drained from the pipeline before introducing steam. There are cases, however, where this may not be feasible.
- A steam pipline that is routed underground to cross a road has a low point in a confined utility sump, and it may not be possible to drain the water safely from this location.
- Where the condensate drain is fully open, but the steam pipeline is at a slight vacuum and prevents the condensate from draining.
- The ground shifts and changes the location of the low point.
There are many practical reasons why condensate can not drained completely from a steam pipeline during warmup.
A novel method to mitigate hammering where steam is introduced to cold water is to blend a small amount of non-condensable gas with the steam (Griffith, 1997). This phenomena was studied by the Nordic Nuclear Safety Research facility (Puustinen, 2007), and the conclusion was that steam containing 1% by volume air eliminated severe hammering where steam is injected into a pool of cold water. I have seen this method used to mitigate hammering on the afore mentioned subcooled condensate line in the Ethylene Plant. A small amount of nitrogen was added to the flashed condensate. This eliminated the shotgun blast voilent hammering and produced a quiet gurgling.
In this work, I investigated the suppression of CIWH in horizontal piping in my back yard in early March 2021. The data collected was evaluated using Short Time Fourier Transform to quantify the amount of hammering.
Experiment Design
I constructed an inexpensive boiler and pipeline in my back yard to demonstrate CIWH. The boiler, shown in the photo below, is a thermosiphon design constructed from ABS piping. Heat is supplied by a 3000 Watt electric element contained in 2″ steel fittings. Boiler water was softened tap water, with two cups of tea (for colour) and a small amount of tri-sodium phosphate (to increase pH) was added. The boiler has a short piece of clear vinyl tubing to indicate the level in the 3″ steam drum, and a tie point for admitting air. The boiler provided several learning experiences in the form of catastrophic failures. These are discussed at the end of this report.
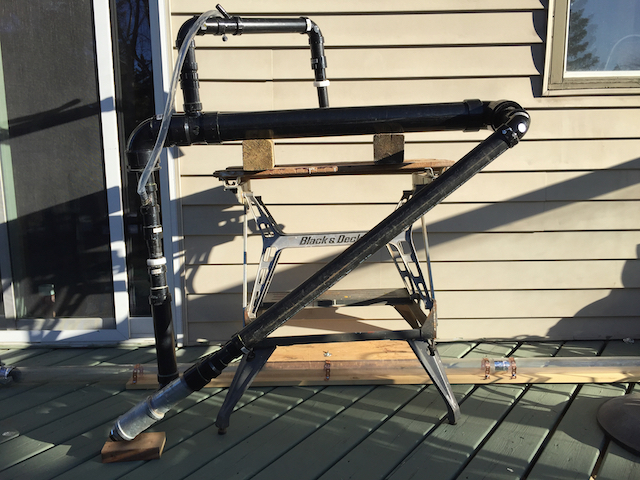
Air was provided by a small bicycle pump. Cold water (assumed to be at 5 C) was provided from the garden hose. The pipeline was 12 feet of 2″ ID clear rigid acrylic tubing. The outlet was partially covered with duct tape to act as a wier and maintain a water level in the pipeline.
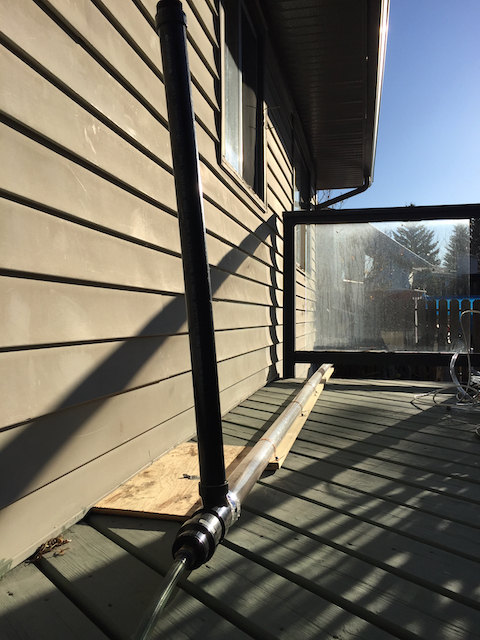
The experiment conditions are tabulated below.
Condition | Value |
---|---|
Elevation | 1160 m (Calgary) |
Atmospheric pressure | 88.1 kPa |
Ambient temperature | 10 C (early March, 2021) |
Steam flow rate | 4.8 kg/h |
Superficial velocity (1-1/2 inch) | 2.0 m/s |
Superficial velocity (2 inch) | 1.2 m/s |
Reynolds Number (1-1/2 inch) | 3400 |
Reynolds Number (2 inch) | 2700 |
Air pump bore and stroke | 25.4 mm diameter x 190 mm long |
Air pumping period | 5 sec |
Air concentration | 1% |
Video of the pipeline was recorded with a webcam connected to a Macbook Air. Measurements of the hammering intensity were obtained as a dedicated audio track, recorded with a Lavelier microphone 1 meter from the pipeline tee. A Chromebook was used to capture the audio track as a 44,100 Hz WAV file. Data analysis and visualization was performed with Python/Jupyter Notebook on the Chromebook.
Two experimental runs were carried out, the first with steam only, and the second with steam containing 1% air. Sound data were recorded for approximately three minutes for each run for quantitiative analysis. Video recordings were used for qualitative analysis.
Raw data
The video recording of the experiment with steam only is shown below.
The raw data for the recorded audio is shown in the upper right of the figure, with an animated line to highlight the part of the audio track that matches the video. The sharp BANGs were similar to the report from a low velocity 22 calibre rifle bullet. The audio track illustrates that most of these events were off-scale when recorded.
The results from adding air at 1% concentration are shown below.
Qualitatively, the events seemed to be somewhat quieter, and this is reflected in the lower amplitude for the sharp bangs on the WAV file. The soft “clicks” that produce an amplitude of 0.5 are caused by the cyclic act on the air pump, not a hammering event.
A Discrete Fourier transform was applied to this data for both cases.
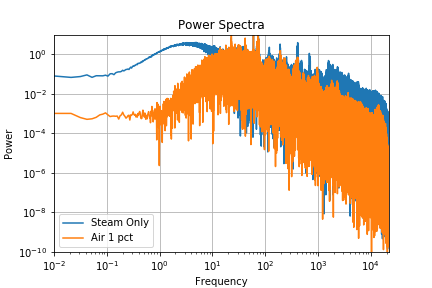
The following points are made from this analysis.
- The complete frequency spectra picks up the hammering with the steam only case as a broad band with frequency less than 1 Hz. This is consistant with the observations of hammering, which has a period of approximately 10 – 20 seconds.
- There are similar signals at approximately 70, 130, 200, 400 Hz. The origin of these patterns is unknown.
- In the range 10 – 1000 Hz, both power spectra areq quite similar. There is a bit more energy in the steam-only case.
- The steam only case has approxmimately 10x the power above 1000 Hz. There is a curious hump in the power spectra at 1300 Hz for steam only, where the air case has a more uniform power spectra. My assumption is this is an artifact of the sharp SNAP when hammering.
Data analysis
A Short Time Fourier Transform (STFT) was used to assess the sound data from the experimental runs. An STFT breaks the transient data into a series of short windows and calculates the frequency spectra for each of the windows. The methodology used is described by Nelson (2014). In this case, the windows consisted of 8192 points (0.19 sec) and were scaled with a half-cosine function. Another 4096 points (zeros) were added as padding on each side. This analysis method demonstrated how the frequency spectra changed during a hammer event.
A complete spectra for a quite window and a hammering instance with no air are provided in the figure below.
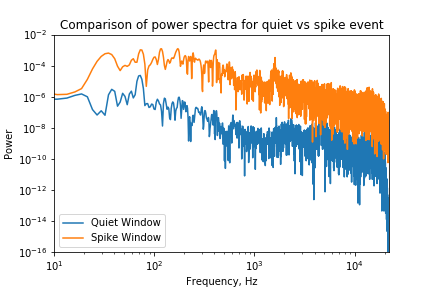
The hammering event caused a fairly uniform increase (by a factor of 100) in the spectral power over all frequencies.
The total amount of energy associated with the hammer event was quantified by integrating the area under the power spectra curve. The total sound power was then calculated as the logarithm of this integrated value.
An animation of the total sound power is shown with the video results for steam only is shown below.
This clearly shows the large spike in sound energy associated with the hammer event. Since the raw data for this run exceeded the measurement scale, the actual sound energy should be somewhat higher than calculated.
The total sound power for the run with air was calculated in the same manner. The animation of the total sound power is shown with the video below.
The figure below shows this result beside the steam-only result for reference.
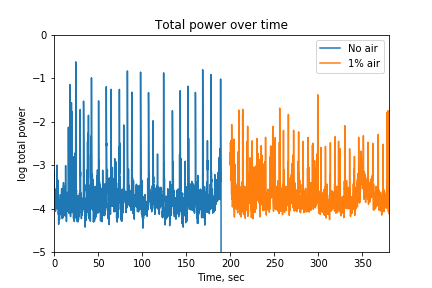
This result shows clearly that the total sound power for the hammer events with air has 1/10 of the energy compared to the hammer events with steam only. Since small amplitude peaks (with 5 second period) are attributed to the noise made by the air pump, it follows that the addition of air suppressed the hammering more than is illustrated in the above figure.
Recommendations
Adding a small amount of air (or other non-condensible gas) should be considered as part of a steam pipeline warmup procedure at atmospheric pressure. The addition of air supresses hammering and guarantees that condensate is displaced through a low-point drain.
The suppression effect of air at higher steam pressures is not known. A simple experimental program should be developed to investigate hammering near typical operating pressures.
Learning Experiences
ABS has a maximum operating temperature of 80 C. The material softened a bit at the 96 C operating temperature, but the glued joints did not come apart. ABS unions, which contain fairly thing pieces of material, failed. Overall, ABS is suitable for this application if the piping is supported and weak fittings are avoided.
The first boiler constructed was a simple kettle, constructed from a 2 ft length of 2″ ABS pipe containing the heating element. There was inadequate heat transfer at the element, which caused the element to overheat, break and short out, and melt holes in the ABS pipe. The simple kettle suffered from two problems. First, the stagnant water in the two inch enclosure prevented water from contacting the heating element, which caused the element to overheat and burn out. Second, the small volume of water did not provide a long run time, and there was no level indication to confirm that the heating element was immersed in water.
These problems were solved. The element enclosure was upgraded to steel fittings, and the design was changed to a thermosiphon boiler with a large steam drum and simple level indication. This was a good approach. However, I over-engineered the piping flexibility and permitted the boiler to be disassembled, and this introduced different failures.
Unions and unglued (taped) joints were used to permit disassembly and allow pipe movement. However, the design had a large mass of steel fittings attached with unions to a long runs of liquid-filled piping. This introduced a lot of stress and the unions failed. The solution was to remove unions, glue all of the joints where possible and forget about disassembling the boiler. The threaded ABS/steel joints would leak, but this was a minor inconvenience.
The liquid velocity in the 1-1/2 inch section of downcomer was estimated to be 2 m/s, and this mass flow rate would certainly be sufficient to ensure good heat transfer for the heating element. The velocity estimate came from the level indication, which was attached to the downcomer. The measured level would periodically drop about 200 mm, and occasionally sucked air into the downcomer. I will leave it as an exercise to the reader to confirm that 200 mm of water head yields a velocity of about 2 m/s. The solution was to throttle the outlet of the boiler by removing the (broken) 2 inch union and replacing it with a short spool of 1-1/2 pipe. Sporadic ingress of air into the liquid level gauge was prevented by attaching the top of level gauge to the air injection port at the steam outlet line.
A union was needed on the steam drum outlet steam line to permit the boiler to be filled with water, and a slip joint was used to connect the steam downcomer to the pipeline tee. Both of these joints would permit air to be sucked in after a hammer produced a vacuum. Thus, the results with no air were probably contaminated with air, and the observed hammering was less violent than it would be with well sealed piping.
Extremely violent hammering was anticipated (hoped for) but not witnessed. The experiment had a limited volume of steam supply piping, and this provided a small amount of energy for the hammering phenomena. A longer run of piping from the boiler to the pipeline would better reflect industrial piping systems, which undergo severe hammering.
The steam flow rate was relatively low, and the Reynolds numbers were barely into the turbulent regime. It is possible that the air was dispersed uniformly in the steam. The solution is to use the maximum possible power for a threaded electric heating element (approx 5500 W) and to reduce the steam line diameter from 1-1/2 inch to 1-1/4 inch.
The low steam rate also caused problems with the initiation of hammering in the horizontal pipeline. The configuration with a half full pipeline should have been conducive to hammering (according to Griffith, 1997), but it was not. The weir height was raised to bring the water level to approximately 80% of the pipe diameter and the water flowrate was increased to produce hammering.
A simpler, more robust boiler design is planned for future experiments.
References
- Griffith, Screening reactor steam/water piping systems for water hammer, NUREG/CR-6519 (1997).
- Puustinen, Combined effects experiments with the condensation pool test facility, NKS-148 (2007).
- ERCB Investigation Report, MEG Energy Corp. Steam Pipeline Failure, IR20080902 (2008).
- Izenson, Rothe, Wallis, Diagnosis of condensation induced waterhammer, NUREG/CR-5220 (1988).
- Kevin Nelson, Short Time Fourier Transform (2014) https://kevinsprojects.wordpress.com/2014/12/13/short-time-fourier-transform-using-python-and-numpy/